16
сен
Using the Mini Modbus board with Mach3. Make sure you select the correct COM port as well as the baudrate you have set on the Mini MODBUS board, the default is 57600, then click. (0 in this case) and select the Serial Plugin Enabled radio button. Look at most relevant Mach3 serial port websites out of 53 Thousand at KeyOptimize.com. Mach3 serial port found at machsupport.com, henriksplace.se, homanndesigns.com. • Plugin for Mach3 software, lets you use the Mach3 through the USB port. • Electrical isolation of USB drivers, protecting your computer. • Voltage Power 24 volts.
Question #: 13375 Question: How to configure 2.2KW VFD for Modbus communication with Mach3 Current Solution It is possible to connect and configure the spindle VFD to the mach3 via an RS485 communication and protocol. The first thing you will need is the dynamic link library to pair with mach3 called the Huanyang VFD Mach3 PlugIn. You will first need to derive the number of turns per inch that your lead screw produces. Programma dlya klyucha indesit 1.
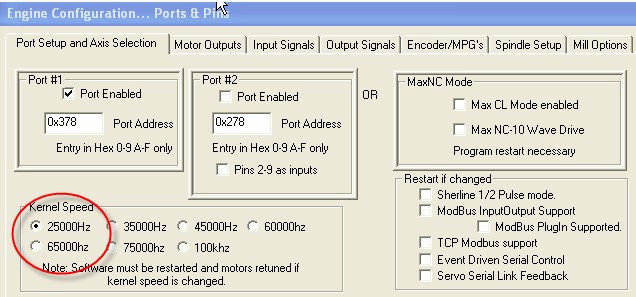
If there is only a single start (typical all thread screws), then the turns per inch is the same as TPI (threads per inch). If there is multiple starts, then the number of starts is divided by the TPI to determine the turns per inch. For example, 10 TPI with 5 starts is 10 / 5 = 2 turns per inch. Now that we know this, we can get the number of steps per inch as described in the previous question: take the number of steps per revolution that the motor will output. This will be the number of full steps that you motor produces (typically 200, or 1.8 degrees per step) multiplied by the microstepping per step to which the driver is configured.
Simply multiple the number of turns per inch and the number of steps per revolution and you will get the steps per inch. Ok, lets see the formula: 200 steps * 16 microsteps * 2 turns per inch = 6400 steps per inch Additional Information: 14798 Additional Information: hallo i have cnc with ball screw 2.5mm of pith.n driver stepping 1/16 how to setup step value Additional Information: i have ball screw with 2.5 mm of pith n 1 start motor 200 step 1/16 driver stepping Click the link to respond: •. First, you will need to know the pitch of the roller chain, or timing belt. For example, #25 roller chain is.25' (1/4') pitch and #40 roller chain is.5' (1/2') pitch.
Timing belts are similar and you will need to search the specifications of your particular drive pulley pitch. Take this pitch and multiply this with the number of teeth on the drive pulley/sprocket.
This will give you the number of inches around the pulley/sprocket. Now, take the number of steps per revolution that the motor will output. This will be the number of full steps that you motor produces (typically 200, or 1.8 degrees per step) multiplied by the microstepping per step to which the driver is configured.
Divide this number by the inches that was calculated from the drive pulley/sprocket. Here is an example: If the motor produces 200 steps per revolution and I am driving it at 1/16 microstepping and my sprocket pitch is.25' with 9 teeth, my formula would be: (200 steps * 16 microsteps) / (.25 inches * 9 teeth) = 3200 steps per revolution / 2.25 inches = 1422.222 steps per inch Click the link to respond: •. The redLeaf CNC computer systems will have either Mach3 or LinuxCNC installed as per the customer's request. If the Mach3 license is purchased, the license file will also be installed on the redLeaf CNC computer system.
The Mach3 or LinuxCNC settings will be configured during the assembly of the system. We contact the customer to determine the drive (mechanics) and inertial (weight of gantry and other parts of the gantry) specifications in order to correctly configure the steps per inch, velocity and acceleration. Click the link to respond: •. It is possible to connect and configure the spindle VFD to the mach3 via an RS485 communication and protocol. The first thing you will need is the dynamic link library to pair with mach3 called the Huanyang VFD Mach3 PlugIn. I noticed in the Computer CNC Systems of this webpage that Linux/EMC2 (now called LinuxCNC) is available on the preconfigured systems.
Popular Posts
Using the Mini Modbus board with Mach3. Make sure you select the correct COM port as well as the baudrate you have set on the Mini MODBUS board, the default is 57600, then click. (0 in this case) and select the Serial Plugin Enabled radio button. Look at most relevant Mach3 serial port websites out of 53 Thousand at KeyOptimize.com. Mach3 serial port found at machsupport.com, henriksplace.se, homanndesigns.com. • Plugin for Mach3 software, lets you use the Mach3 through the USB port. • Electrical isolation of USB drivers, protecting your computer. • Voltage Power 24 volts.
Question #: 13375 Question: How to configure 2.2KW VFD for Modbus communication with Mach3 Current Solution It is possible to connect and configure the spindle VFD to the mach3 via an RS485 communication and protocol. The first thing you will need is the dynamic link library to pair with mach3 called the Huanyang VFD Mach3 PlugIn. You will first need to derive the number of turns per inch that your lead screw produces. Programma dlya klyucha indesit 1.
If there is only a single start (typical all thread screws), then the turns per inch is the same as TPI (threads per inch). If there is multiple starts, then the number of starts is divided by the TPI to determine the turns per inch. For example, 10 TPI with 5 starts is 10 / 5 = 2 turns per inch. Now that we know this, we can get the number of steps per inch as described in the previous question: take the number of steps per revolution that the motor will output. This will be the number of full steps that you motor produces (typically 200, or 1.8 degrees per step) multiplied by the microstepping per step to which the driver is configured.
Simply multiple the number of turns per inch and the number of steps per revolution and you will get the steps per inch. Ok, lets see the formula: 200 steps * 16 microsteps * 2 turns per inch = 6400 steps per inch Additional Information: 14798 Additional Information: hallo i have cnc with ball screw 2.5mm of pith.n driver stepping 1/16 how to setup step value Additional Information: i have ball screw with 2.5 mm of pith n 1 start motor 200 step 1/16 driver stepping Click the link to respond: •. First, you will need to know the pitch of the roller chain, or timing belt. For example, #25 roller chain is.25\' (1/4\') pitch and #40 roller chain is.5\' (1/2\') pitch.
Timing belts are similar and you will need to search the specifications of your particular drive pulley pitch. Take this pitch and multiply this with the number of teeth on the drive pulley/sprocket.
This will give you the number of inches around the pulley/sprocket. Now, take the number of steps per revolution that the motor will output. This will be the number of full steps that you motor produces (typically 200, or 1.8 degrees per step) multiplied by the microstepping per step to which the driver is configured.
Divide this number by the inches that was calculated from the drive pulley/sprocket. Here is an example: If the motor produces 200 steps per revolution and I am driving it at 1/16 microstepping and my sprocket pitch is.25\' with 9 teeth, my formula would be: (200 steps * 16 microsteps) / (.25 inches * 9 teeth) = 3200 steps per revolution / 2.25 inches = 1422.222 steps per inch Click the link to respond: •. The redLeaf CNC computer systems will have either Mach3 or LinuxCNC installed as per the customer\'s request. If the Mach3 license is purchased, the license file will also be installed on the redLeaf CNC computer system.
The Mach3 or LinuxCNC settings will be configured during the assembly of the system. We contact the customer to determine the drive (mechanics) and inertial (weight of gantry and other parts of the gantry) specifications in order to correctly configure the steps per inch, velocity and acceleration. Click the link to respond: •. It is possible to connect and configure the spindle VFD to the mach3 via an RS485 communication and protocol. The first thing you will need is the dynamic link library to pair with mach3 called the Huanyang VFD Mach3 PlugIn. I noticed in the Computer CNC Systems of this webpage that Linux/EMC2 (now called LinuxCNC) is available on the preconfigured systems.
...'>Mach3 Serial Port Plugin Container(16.09.2018)Using the Mini Modbus board with Mach3. Make sure you select the correct COM port as well as the baudrate you have set on the Mini MODBUS board, the default is 57600, then click. (0 in this case) and select the Serial Plugin Enabled radio button. Look at most relevant Mach3 serial port websites out of 53 Thousand at KeyOptimize.com. Mach3 serial port found at machsupport.com, henriksplace.se, homanndesigns.com. • Plugin for Mach3 software, lets you use the Mach3 through the USB port. • Electrical isolation of USB drivers, protecting your computer. • Voltage Power 24 volts.
Question #: 13375 Question: How to configure 2.2KW VFD for Modbus communication with Mach3 Current Solution It is possible to connect and configure the spindle VFD to the mach3 via an RS485 communication and protocol. The first thing you will need is the dynamic link library to pair with mach3 called the Huanyang VFD Mach3 PlugIn. You will first need to derive the number of turns per inch that your lead screw produces. Programma dlya klyucha indesit 1.
If there is only a single start (typical all thread screws), then the turns per inch is the same as TPI (threads per inch). If there is multiple starts, then the number of starts is divided by the TPI to determine the turns per inch. For example, 10 TPI with 5 starts is 10 / 5 = 2 turns per inch. Now that we know this, we can get the number of steps per inch as described in the previous question: take the number of steps per revolution that the motor will output. This will be the number of full steps that you motor produces (typically 200, or 1.8 degrees per step) multiplied by the microstepping per step to which the driver is configured.
Simply multiple the number of turns per inch and the number of steps per revolution and you will get the steps per inch. Ok, lets see the formula: 200 steps * 16 microsteps * 2 turns per inch = 6400 steps per inch Additional Information: 14798 Additional Information: hallo i have cnc with ball screw 2.5mm of pith.n driver stepping 1/16 how to setup step value Additional Information: i have ball screw with 2.5 mm of pith n 1 start motor 200 step 1/16 driver stepping Click the link to respond: •. First, you will need to know the pitch of the roller chain, or timing belt. For example, #25 roller chain is.25\' (1/4\') pitch and #40 roller chain is.5\' (1/2\') pitch.
Timing belts are similar and you will need to search the specifications of your particular drive pulley pitch. Take this pitch and multiply this with the number of teeth on the drive pulley/sprocket.
This will give you the number of inches around the pulley/sprocket. Now, take the number of steps per revolution that the motor will output. This will be the number of full steps that you motor produces (typically 200, or 1.8 degrees per step) multiplied by the microstepping per step to which the driver is configured.
Divide this number by the inches that was calculated from the drive pulley/sprocket. Here is an example: If the motor produces 200 steps per revolution and I am driving it at 1/16 microstepping and my sprocket pitch is.25\' with 9 teeth, my formula would be: (200 steps * 16 microsteps) / (.25 inches * 9 teeth) = 3200 steps per revolution / 2.25 inches = 1422.222 steps per inch Click the link to respond: •. The redLeaf CNC computer systems will have either Mach3 or LinuxCNC installed as per the customer\'s request. If the Mach3 license is purchased, the license file will also be installed on the redLeaf CNC computer system.
The Mach3 or LinuxCNC settings will be configured during the assembly of the system. We contact the customer to determine the drive (mechanics) and inertial (weight of gantry and other parts of the gantry) specifications in order to correctly configure the steps per inch, velocity and acceleration. Click the link to respond: •. It is possible to connect and configure the spindle VFD to the mach3 via an RS485 communication and protocol. The first thing you will need is the dynamic link library to pair with mach3 called the Huanyang VFD Mach3 PlugIn. I noticed in the Computer CNC Systems of this webpage that Linux/EMC2 (now called LinuxCNC) is available on the preconfigured systems.
...'>Mach3 Serial Port Plugin Container(16.09.2018)